Mastering Pipeline Design with AutoPIPE: A Comprehensive Guide
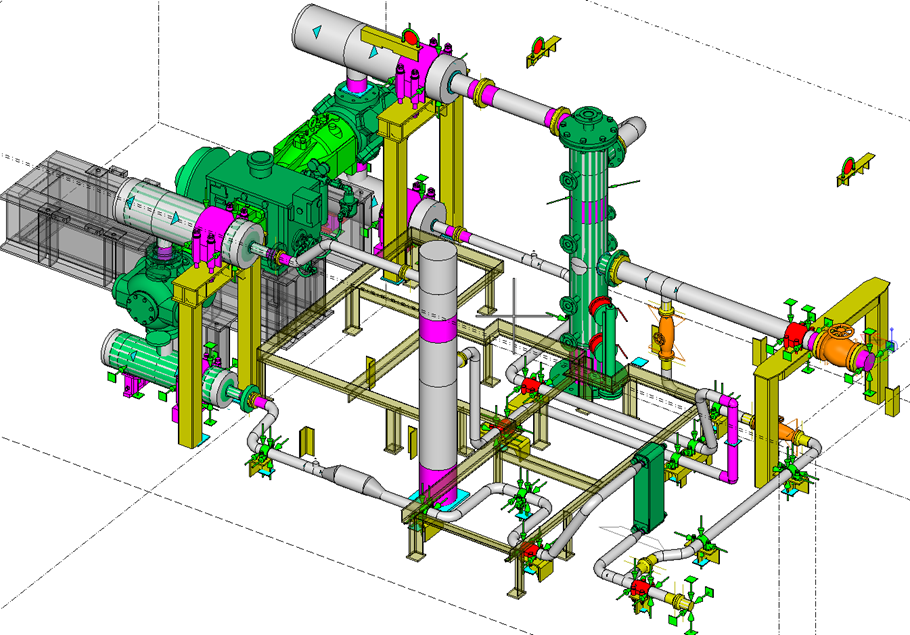
Introduction: Designing pipelines is a critical aspect of engineering in industries such as oil and gas, petrochemical, and infrastructure development. AutoPIPE is a leading software tool used by engineers and designers for the analysis and design of pipelines and piping systems. With its advanced capabilities for stress analysis, code compliance, and optimization, AutoPIPE enables engineers to ensure the structural integrity and safety of pipeline systems. In this comprehensive guide, we’ll delve deep into the intricacies of designing pipelines in AutoPIPE, covering everything from model setup to analysis and optimization.
Section 1: Introduction to AutoPIPE 1.1 Overview of AutoPIPE: AutoPIPE is a comprehensive software solution developed by Bentley Systems for the analysis and design of piping systems. It provides engineers with tools for modeling, analyzing, and evaluating the performance of pipelines and piping networks. AutoPIPE offers advanced capabilities for stress analysis, code compliance checking, dynamic analysis, and fatigue assessment, making it a versatile tool for pipeline design and engineering.
1.2 Key Features of AutoPIPE: AutoPIPE offers a range of features designed to streamline the pipeline design process. These include intuitive modeling tools for creating 3D models of piping systems, advanced analysis capabilities for assessing structural integrity and safety, comprehensive material and component libraries, and integration with other engineering software packages. AutoPIPE’s user-friendly interface and powerful analysis tools make it a preferred choice for engineers and designers in the pipeline industry.
Section 2: Setting Up Pipeline Models in AutoPIPE 2.1 Defining Geometry and Components: The first step in designing pipelines in AutoPIPE is to define the geometry and components of the pipeline system. Engineers can use AutoPIPE’s modeling tools to create 3D models of pipelines, including straight sections, bends, fittings, and supports. AutoPIPE provides a library of standard pipe components and allows engineers to define custom components as needed.
2.2 Specifying Material Properties and Loads: Once the geometry is defined, engineers must specify the material properties and loads acting on the pipeline system. AutoPIPE allows engineers to define material properties such as Young’s modulus, Poisson’s ratio, and yield strength for each pipe component. Engineers can also specify loads such as internal pressure, temperature, and deadweight loads, as well as external loads such as wind, seismic, and thermal expansion loads.
Section 3: Performing Stress Analysis and Code Compliance Checking 3.1 Stress Analysis: AutoPIPE performs stress analysis to assess the structural integrity of the pipeline system and ensure that it can withstand the loads and operating conditions it is subjected to. AutoPIPE calculates stresses and strains in the pipeline components using finite element analysis techniques and checks them against code-defined allowable limits. Engineers can visualize stress distributions and identify critical locations where stress concentrations occur.
3.2 Code Compliance Checking: AutoPIPE checks the pipeline design against various industry codes and standards to ensure compliance with safety and regulatory requirements. These codes include ASME B31.1, ASME B31.3, ASME B31.4, ASME B31.8, and others. AutoPIPE performs code compliance checks for factors such as stress, displacement, fatigue, and stability, and provides detailed reports highlighting areas of non-compliance that require attention.
Section 4: Dynamic Analysis and Fatigue Assessment 4.1 Dynamic Analysis: AutoPIPE allows engineers to perform dynamic analysis to evaluate the response of the pipeline system to dynamic loads such as water hammer, vibration, and seismic events. Dynamic analysis helps engineers assess the dynamic behavior of the pipeline system and identify potential resonance, instability, or fatigue issues that may arise under transient loading conditions.
4.2 Fatigue Assessment: Fatigue assessment is critical for ensuring the long-term structural integrity of pipeline systems, especially in applications subject to cyclic loading. AutoPIPE calculates fatigue life estimates for pipeline components based on stress ranges and material fatigue properties. Engineers can use fatigue assessment results to identify components prone to fatigue failure and implement mitigation measures such as design modifications or material selection.
Section 5: Optimization and Design Validation 5.1 Design Optimization: AutoPIPE provides optimization tools that allow engineers to optimize pipeline designs for performance, cost, and safety. Engineers can iterate on the design parameters such as pipe diameter, wall thickness, support spacing, and material selection to achieve optimal design solutions. AutoPIPE’s optimization capabilities help engineers balance competing design objectives and achieve designs that meet all requirements.
5.2 Design Validation: Once the pipeline design is optimized, engineers must validate the design through testing and analysis to ensure its safety and reliability. AutoPIPE provides validation tools that allow engineers to compare simulation results with experimental data or analytical solutions. Engineers can perform sensitivity analysis and what-if scenarios to assess the impact of design parameters on performance and identify areas for improvement.
Conclusion: Designing pipelines is a complex and critical task that requires careful consideration of various factors such as structural integrity, safety, and regulatory compliance. AutoPIPE provides engineers with the tools and capabilities needed to model, analyze, and optimize pipeline designs efficiently and effectively. By mastering the techniques outlined in this guide and leveraging the capabilities of AutoPIPE, engineers can design pipeline systems that meet the highest standards of safety, reliability, and performance in the oil and gas, petrochemical, and infrastructure industries.