Mastering Chemical Process Modeling with Aspen Plus: A Comprehensive Guide
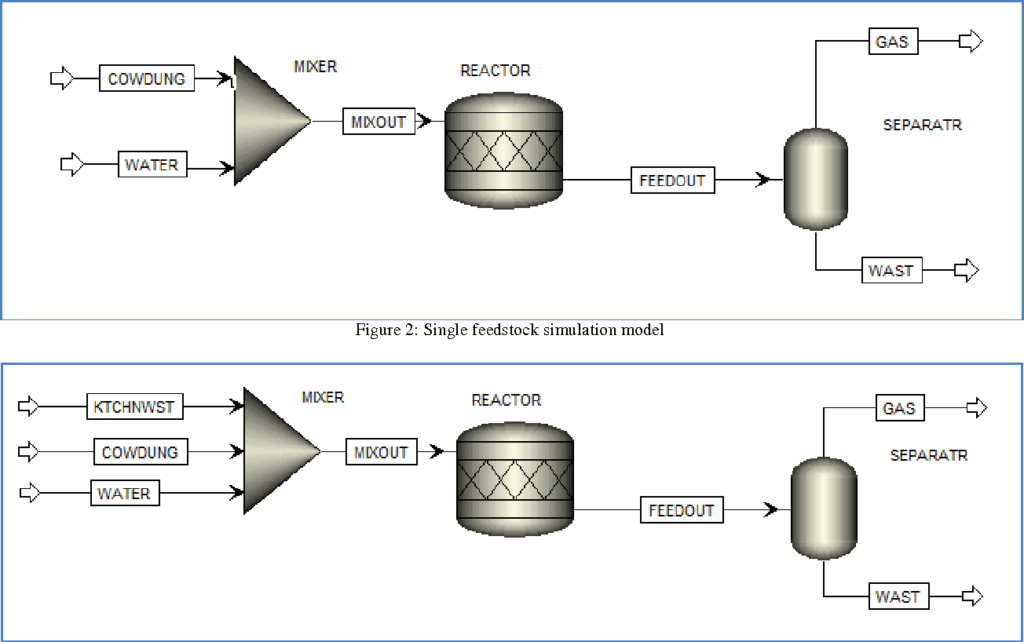
Introduction: Aspen Plus is a leading process simulation software used by chemical engineers and researchers to model, simulate, and optimize chemical processes. With its comprehensive suite of tools for thermodynamic modeling, reaction kinetics, and process optimization, Aspen Plus enables engineers to design and analyze complex chemical processes efficiently. In this comprehensive guide, we’ll delve deep into the intricacies of modeling chemical processes in Aspen Plus, covering everything from process setup to simulation and optimization.
Section 1: Introduction to Aspen Plus 1.1 Overview of Aspen Plus: Aspen Plus is a process simulation software developed by AspenTech that allows engineers to model and simulate chemical processes in various industries, including petrochemicals, pharmaceuticals, and environmental engineering. Aspen Plus uses a rigorous thermodynamic framework to model phase equilibrium, chemical reactions, heat and mass transfer, and other phenomena relevant to chemical processes.
1.2 Key Features of Aspen Plus: Aspen Plus offers a range of features designed to streamline the process modeling workflow. These include a comprehensive thermodynamic database, customizable unit operation models, built-in reaction kinetics, optimization tools, and integration with other AspenTech software products. Engineers can use Aspen Plus to model a wide variety of chemical processes, from simple unit operations to complex chemical reactors and process flowsheets.
Section 2: Setting Up Chemical Process Models in Aspen Plus 2.1 Defining Process Flowsheets: The first step in modeling chemical processes in Aspen Plus is to define the process flowsheet, which represents the sequence of unit operations and streams within the process. Engineers can use Aspen Plus’s graphical user interface to build the flowsheet by selecting and connecting unit operation blocks such as reactors, separators, and heat exchangers.
2.2 Specifying Process Conditions and Stream Properties: Once the flowsheet is defined, engineers must specify the operating conditions and stream properties for each unit operation in the process. This includes defining temperature, pressure, flow rates, compositions, and physical properties for each process stream. Engineers can use Aspen Plus’s built-in property methods and thermodynamic models to estimate stream properties accurately.
Section 3: Modeling Chemical Reactions and Kinetics 3.1 Defining Reaction Chemistry: Chemical reactions play a central role in many chemical processes, and Aspen Plus provides tools for modeling and simulating reaction kinetics accurately. Engineers can define reaction chemistry using Aspen Plus’s reaction editor, specifying reaction stoichiometry, kinetics, and thermodynamics for each chemical reaction in the process.
3.2 Reaction Kinetics and Rate Laws: Aspen Plus supports a variety of reaction kinetics models, including elementary reactions, lumped kinetics, and user-defined rate laws. Engineers can choose the appropriate kinetic model based on the reaction mechanism and experimental data available for the system. Aspen Plus’s reaction kinetics solver solves the reaction rate equations numerically to predict reaction rates and product concentrations over time.
Section 4: Simulating Chemical Processes and Analyzing Results 4.1 Running Simulations: Once the process model is set up, engineers can run simulations in Aspen Plus to predict the behavior of the chemical process under different operating conditions. Aspen Plus solves the mass and energy balance equations for the process flowsheet, taking into account phase equilibrium, reaction kinetics, heat and mass transfer, and other phenomena.
4.2 Analyzing Simulation Results: After simulation, engineers can analyze the results to gain insights into the behavior of the chemical process. Aspen Plus provides visualization tools for plotting process variables, including temperature profiles, concentration profiles, flow rates, and conversion rates. Engineers can use these results to assess process performance, identify bottlenecks, and optimize operating conditions.
Section 5: Optimization and Process Design 5.1 Process Optimization: Aspen Plus offers optimization tools that allow engineers to optimize process performance and design parameters automatically. Engineers can define optimization objectives, constraints, and decision variables using Aspen Plus’s optimization interface. Aspen Plus’s optimization solver searches for optimal solutions by varying process parameters and evaluating the objective function iteratively.
5.2 Sensitivity Analysis and What-If Scenarios: Engineers can perform sensitivity analysis and what-if scenarios in Aspen Plus to assess the impact of process parameters on performance and profitability. By varying input parameters such as feed compositions, operating conditions, and reactor configurations, engineers can evaluate the sensitivity of process variables and identify critical factors influencing process performance.
Conclusion: Aspen Plus is a powerful tool for modeling, simulating, and optimizing chemical processes in various industries. By mastering the techniques outlined in this guide and leveraging the capabilities of Aspen Plus, engineers can design and analyze complex chemical processes efficiently, optimize process performance, and develop innovative solutions to engineering challenges. With its intuitive interface, comprehensive thermodynamic models, and advanced simulation and optimization tools, Aspen Plus empowers engineers to tackle a wide range of chemical process modeling tasks with confidence and precision.