Mastering Efficiency: A Comprehensive Guide to Analyzing Toolpaths in PowerMill Ultimate
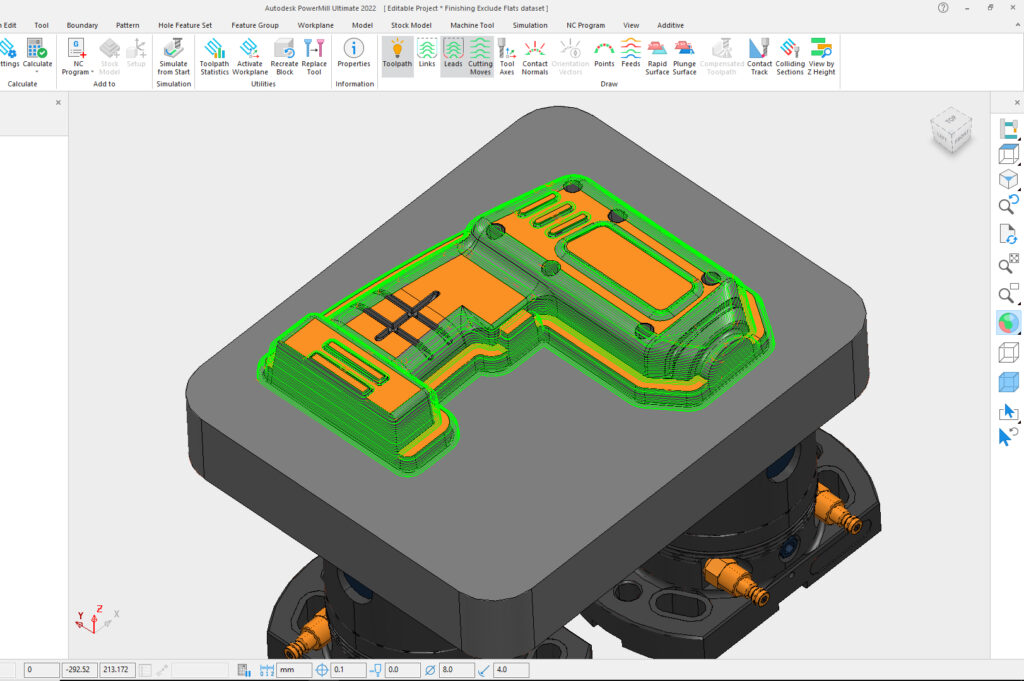
In the realm of computer-aided manufacturing (CAM) software, PowerMill Ultimate stands out as a powerhouse, offering advanced capabilities for generating toolpaths that drive CNC machines to produce intricate and precise parts. However, the efficiency of these toolpaths can significantly impact manufacturing productivity, cost-effectiveness, and overall quality. To unlock the full potential of PowerMill Ultimate, mastering the art of analyzing toolpaths for efficiency is paramount.
Understanding Toolpaths in PowerMill Ultimate
Before delving into the intricacies of analyzing toolpaths, it’s crucial to grasp the fundamentals of how PowerMill Ultimate generates and manipulates them. At its core, PowerMill Ultimate utilizes sophisticated algorithms to calculate toolpaths based on various parameters such as tool geometry, part geometry, machining strategies, and material properties.
Toolpaths in PowerMill Ultimate are typically represented in three dimensions, with each axis dictating the movement of the cutting tool during machining. These toolpaths can be categorized into different types, including roughing, finishing, and rest machining, each serving a specific purpose in the manufacturing process.
The Importance of Efficiency in Toolpath Analysis
Efficiency in toolpath analysis refers to the optimization of machining operations to achieve maximum productivity with minimal resources and time. In the context of PowerMill Ultimate, analyzing toolpaths for efficiency entails evaluating various factors such as machining time, tool wear, material removal rates, surface finish, and overall production costs.
By identifying inefficiencies and optimizing toolpaths accordingly, manufacturers can streamline their operations, reduce machining cycle times, minimize tooling costs, and ultimately enhance the competitiveness of their products in the market.
Key Metrics for Analyzing Toolpaths
To conduct a comprehensive analysis of toolpaths in PowerMill Ultimate, it’s essential to focus on several key metrics:
- Machining Time: The total time required to complete a machining operation, including tool changes, toolpath transitions, and material removal.
- Tool Wear: The rate at which cutting tools degrade during machining, influenced by factors such as cutting speed, feed rate, tool material, and workpiece material.
- Material Removal Rate (MRR): The volume of material removed per unit of time, indicating the efficiency of the machining process in removing excess material.
- Surface Finish: The quality and smoothness of the machined surface, influenced by factors such as toolpath strategy, cutting parameters, and toolpath overlap.
- Toolpath Optimization: The process of refining toolpaths to minimize unnecessary movements, reduce air cutting, and optimize tool engagement for improved efficiency.
Tools and Techniques for Analyzing Toolpaths
PowerMill Ultimate offers a range of tools and techniques for analyzing and optimizing toolpaths:
- Simulation: Utilize the built-in simulation capabilities of PowerMill Ultimate to visualize toolpaths, simulate machining operations, and identify potential collisions or errors.
- Collision Detection: Employ collision detection algorithms to identify and rectify instances where the tool, tool holder, or machine may collide with the workpiece or fixtures during machining.
- Toolpath Tracing: Trace the toolpath trajectory to identify areas of redundant or inefficient machining, allowing for adjustments to be made to optimize the toolpath.
- Material Removal Simulation: Simulate material removal to visualize the efficiency of the machining process and identify areas of potential improvement.
- Parameter Optimization: Experiment with different cutting parameters such as cutting speed, feed rate, stepover, and depth of cut to optimize toolpaths for maximum efficiency while maintaining part quality.
Best Practices for Analyzing Toolpaths in PowerMill Ultimate
To harness the full potential of PowerMill Ultimate and achieve optimal efficiency in toolpath analysis, consider the following best practices:
- Iterative Optimization: Approach toolpath analysis as an iterative process, continuously refining and optimizing toolpaths based on feedback from simulations, machining trials, and performance metrics.
- Collaboration: Foster collaboration between CAM programmers, machinists, and engineers to leverage their collective expertise in analyzing toolpaths and implementing optimizations.
- Utilize Templates and Macros: Take advantage of pre-defined templates and macros within PowerMill Ultimate to streamline the toolpath generation process and ensure consistency across machining operations.
- Stay Updated: Regularly update PowerMill Ultimate to access the latest features, enhancements, and performance improvements that can further enhance efficiency in toolpath analysis.
- Training and Education: Invest in training and education for CAM programmers and operators to ensure they have the necessary skills and knowledge to effectively analyze and optimize toolpaths in PowerMill Ultimate.
Conclusion
Efficiency in toolpath analysis is the cornerstone of successful manufacturing operations in PowerMill Ultimate. By leveraging advanced simulation tools, optimization techniques, and best practices, manufacturers can unlock new levels of productivity, cost-effectiveness, and quality in their machining processes. With a comprehensive understanding of toolpath analysis and a commitment to continuous improvement, PowerMill Ultimate users can stay ahead of the competition and drive innovation in the ever-evolving landscape of computer-aided manufacturing.