PowerMill Ultimate: Breathing New Life into Material – A Comprehensive Guide to Rest Machining Toolpaths
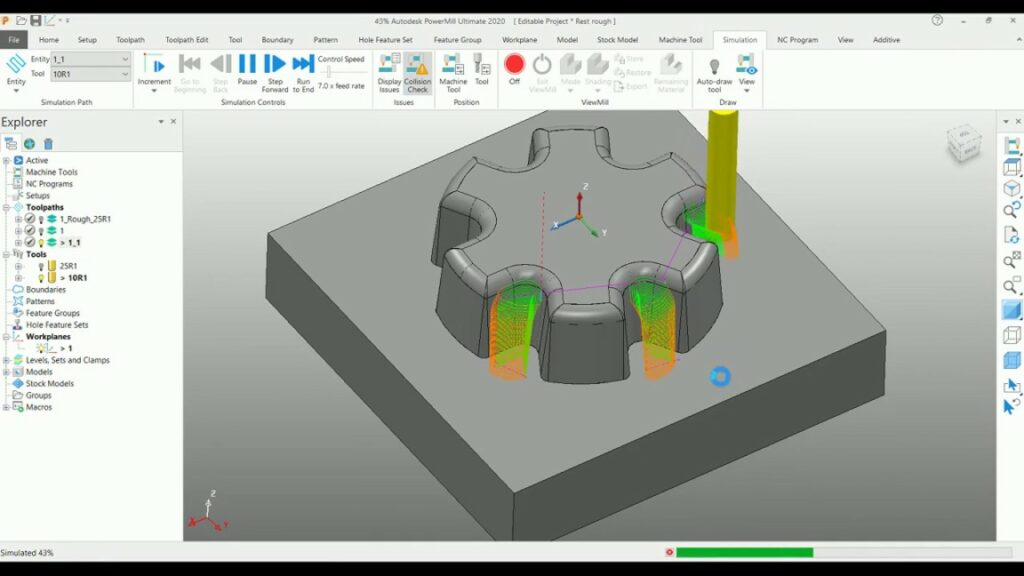
In the realm of CNC machining, maximizing material utilization and minimizing waste are paramount concerns. Rest machining, a powerful technique employed in PowerMill Ultimate, allows you to efficiently machine features within previously machined areas, effectively extracting valuable parts from leftover stock. This comprehensive guide delves into the world of rest machining toolpaths in PowerMill Ultimate, equipping you with the knowledge and techniques to transform leftover material into high-quality finished parts.
Understanding the Rest Machining Workflow: A Step-by-Step Breakdown
Rest machining involves a distinct workflow within PowerMill Ultimate:
Stock Model Creation: The foundation of rest machining is a precise representation of the remaining stock material. This is achieved by creating a “Stock Model” within PowerMill. This model can be generated from the original CAD model by virtually removing the previously machined features. Alternatively, PowerMill can import the stock model from a scan of the actual leftover material.
Defining Rest Geometry: Once you have the stock model, you need to define the remaining material that requires machining. This involves creating “Rest Boundaries” which essentially define the “islands” of material within the stock that will be machined into finished parts. PowerMill offers various methods for creating rest boundaries, including:
- Automatic Rest Boundary Generation: PowerMill can automatically generate rest boundaries based on the stock model and existing toolpaths. This option works well for simple geometries.
- Manual Rest Boundary Creation: For more complex geometries, PowerMill allows for manual definition of rest boundaries using various tools like offset surfaces, trimming, and boolean operations.
Toolpath Generation for Rest Features: With the rest geometry defined, you can generate toolpaths specifically designed to machine the features within the remaining stock. PowerMill offers a variety of toolpath strategies suitable for rest machining, including:
- 3D Roughing and Finishing: These standard toolpath strategies can be applied within the confines of the defined rest boundaries to remove material and achieve the desired final geometry.
- Flowline Milling: A specialized toolpath strategy specifically designed for rest machining. Flowline milling follows a smooth, continuous path around the rest geometry, minimizing tool travel time and optimizing machining efficiency.
Collision Avoidance and Verification: Since rest machining often involves complex geometries and tight clearances, meticulous collision avoidance checks are crucial. PowerMill’s collision detection functionalities ensure the toolpath doesn’t interfere with clamps, fixtures, or other machine components during machining. Additionally, simulation tools allow you to visualize the rest machining process and identify any potential issues before executing the actual machining operation.
By following this step-by-step breakdown, you can effectively utilize rest machining toolpaths in PowerMill Ultimate to breathe new life into leftover material and maximize your material utilization.
Optimizing Rest Machining Strategies: Techniques for Efficiency and Quality
Here are some key considerations to optimize your rest machining strategies in PowerMill Ultimate:
Stock Model Accuracy: The accuracy of your stock model directly impacts the efficiency and effectiveness of your rest machining toolpaths. Ensure the stock model accurately reflects the actual remaining material to avoid tool collisions or incomplete machining.
Rest Boundary Definition: Meticulously define your rest boundaries to ensure they encompass all the features requiring machining while minimizing unnecessary air cutting. This optimizes toolpath efficiency and minimizes machining time.
Tool Selection: Selecting the appropriate cutting tools for rest machining is crucial. Consider factors like tool reach, chip evacuation capabilities, and suitability for tight corners and complex geometries. PowerMill’s library of tools offers various options specifically designed for rest machining applications.
Toolpath Optimization: Utilize PowerMill’s toolpath optimization functionalities to minimize tool travel time and optimize cutting efficiency within the confines of the defined rest boundaries. Techniques like toolpath chaining and minimizing retracts can significantly reduce machining time.
Cooling and Chip Evacuation: Rest machining often involves intricate geometries and tight clearances. Pay close attention to coolant selection and chip evacuation strategies to prevent chip buildup and thermal issues that can negatively impact surface finish and tool life.
By implementing these optimization techniques, you can ensure your rest machining toolpaths are not only efficient but also deliver high-quality parts from what might otherwise be considered scrap material.
The Future of Rest Machining: Embracing Automation and Advanced Techniques
The future of rest machining in PowerMill Ultimate is brimming with exciting possibilities:
Automated Stock Model Generation: Advancements in scanning and 3D modeling technologies might lead to automated generation of stock models directly from leftover material, streamlining the rest machining workflow.
AI-Powered Toolpath Optimization: Artificial intelligence algorithms could analyze the stock model and rest geometry, suggesting optimal toolpath strategies and cutting parameters for even more efficient and effective rest machining processes.