Mastering Noise and Vibration Analysis in Siemens LMS Test.Lab: A Comprehensive Guide
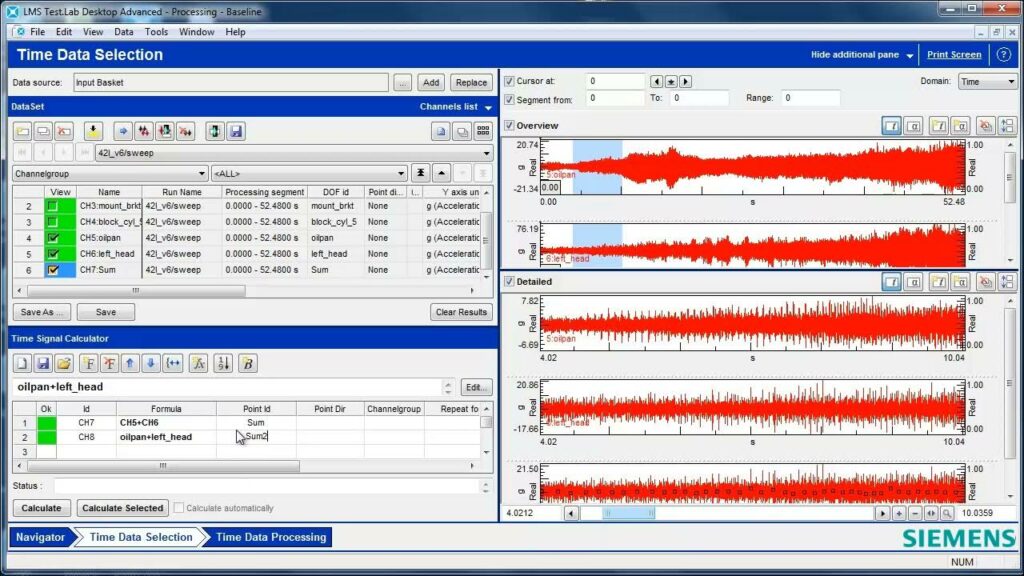
Introduction: Noise and vibration analysis is essential for evaluating the performance, reliability, and comfort of various mechanical systems, including automotive vehicles, aerospace structures, industrial machinery, and consumer products. Siemens LMS Test.Lab is a leading software solution for conducting noise and vibration testing, analysis, and optimization. In this comprehensive guide, we will explore the intricacies of performing noise and vibration analysis in Siemens LMS Test.Lab, covering everything from data acquisition to signal processing and result interpretation.
Section 1: Understanding Noise and Vibration Analysis
1.1 Overview of Noise and Vibration: Noise and vibration are mechanical phenomena that result from the motion of structures and components. Noise refers to unwanted sound generated by vibrating sources, while vibration refers to the oscillatory motion of mechanical systems. Both noise and vibration can have detrimental effects on performance, durability, and user experience if not properly managed and controlled.
1.2 Importance of Analysis: Noise and vibration analysis is crucial for identifying root causes, quantifying levels, and mitigating sources of noise and vibration in mechanical systems. By analyzing frequency spectra, amplitude distributions, and time-domain signals, engineers can diagnose issues, optimize designs, and improve the performance, reliability, and comfort of products and systems.
1.3 Applications of Analysis: Noise and vibration analysis find applications in various industries and domains, including automotive, aerospace, manufacturing, transportation, and consumer goods. Engineers use analysis techniques to evaluate structural integrity, assess dynamic behavior, predict fatigue life, and comply with regulatory standards and customer requirements.
Section 2: Introduction to Siemens LMS Test.Lab Software
2.1 Overview of LMS Test.Lab: LMS Test.Lab is a comprehensive software platform developed by Siemens for noise and vibration testing, analysis, and engineering. It offers a wide range of features and capabilities for data acquisition, signal processing, modal analysis, frequency response analysis, and structural dynamics simulation, making it a versatile tool for engineers and researchers.
2.2 LMS Test.Lab Modules: LMS Test.Lab consists of modular software packages that cater to specific testing and analysis needs, including Sound Quality, Structural Dynamics, Acoustics, Modal Analysis, and Rotating Machinery. Each module provides specialized tools and workflows for conducting specific types of tests and analyses, ensuring flexibility and scalability in application.
2.3 Benefits of Using LMS Test.Lab: LMS Test.Lab provides several benefits for engineers and analysts involved in noise and vibration analysis, including intuitive user interface, advanced analysis algorithms, seamless data integration, and comprehensive reporting capabilities. It enables users to streamline testing processes, accelerate analysis workflows, and make informed decisions based on accurate and reliable results.
Section 3: Performing Noise and Vibration Analysis in LMS Test.Lab
3.1 Data Acquisition: Engineers begin by acquiring experimental data using sensors, transducers, and measurement equipment connected to LMS Test.Lab. They configure measurement channels, set sampling rates, and define trigger conditions to capture relevant signals such as accelerations, velocities, forces, pressures, and sound pressure levels.
3.2 Signal Processing: LMS Test.Lab offers a suite of signal processing tools for pre-processing, filtering, and analyzing acquired data. Engineers apply time-domain and frequency-domain techniques such as Fourier transform, filtering, windowing, averaging, and spectral analysis to extract relevant information, remove noise, and enhance signal clarity.
3.3 Modal Analysis: Modal analysis in LMS Test.Lab aims to identify and characterize the dynamic properties of mechanical structures, including natural frequencies, mode shapes, damping ratios, and modal masses. Engineers perform modal testing, curve fitting, and modal parameter estimation to create modal models and validate finite element models (FEM) for structural dynamics simulation.
Section 4: Advanced Techniques and Optimization Strategies
4.1 Frequency Response Analysis: Frequency response analysis in LMS Test.Lab evaluates the dynamic behavior of mechanical systems under excitation at different frequencies. Engineers analyze frequency response functions, transfer functions, coherence functions, and phase responses to assess system performance, identify resonances, and optimize design parameters for desired specifications.
4.2 Operational Deflection Shapes (ODS): Operational deflection shapes analysis in LMS Test.Lab visualizes the dynamic behavior of structures under operational conditions. Engineers use animation, shape tracking, and video processing techniques to visualize mode shapes, displacement patterns, and deformation modes in real-time, enabling them to diagnose issues, validate simulations, and optimize designs.
4.3 Sound Quality Analysis: Sound quality analysis in LMS Test.Lab evaluates the subjective perception of sound attributes such as loudness, pitch, roughness, and tonality. Engineers use psychoacoustic metrics, sound quality indices, and preference ratings to assess sound quality, identify annoying noises, and optimize sound characteristics for enhanced user experience and comfort.
Section 5: Best Practices and Tips for LMS Test.Lab Analysis
5.1 Sensor Placement and Setup: Place sensors strategically and ensure proper sensor orientation and alignment to capture accurate and representative data during testing. Follow best practices for sensor mounting, attachment, and calibration to minimize measurement errors and ensure reliable results for analysis and interpretation.
5.2 Data Validation and Verification: Validate experimental data against theoretical models, analytical predictions, or reference measurements to ensure accuracy and reliability of analysis results. Compare measured data with simulated data, conduct sensitivity analyses, and perform uncertainty assessments to quantify measurement uncertainties and validate analysis assumptions.
5.3 Model Correlation and Validation: Correlate experimental data with simulation models, finite element models (FEM), or computational models to validate model predictions and ensure model accuracy. Use modal assurance criteria (MAC), mode shape comparisons, and frequency response validations to assess model fidelity, identify discrepancies, and improve model accuracy for analysis and simulation.
Conclusion: Performing noise and vibration analysis in Siemens LMS Test.Lab provides engineers and analysts with a powerful tool for evaluating and optimizing the performance, reliability, and comfort of mechanical systems. By mastering the principles, techniques, and best practices discussed in this guide, engineers can leverage LMS Test.Lab to conduct comprehensive testing, analyze complex data, and make informed decisions to address noise and vibration issues and improve product and system performance. With its advanced analysis capabilities, intuitive user interface, and seamless integration with measurement hardware, LMS Test.Lab continues to be a trusted platform for noise and vibration analysis in industries ranging from automotive and aerospace to manufacturing and consumer goods, empowering users to achieve excellence in noise and vibration engineering.