How to Implement Contact Mechanics in ANSYS Simulations
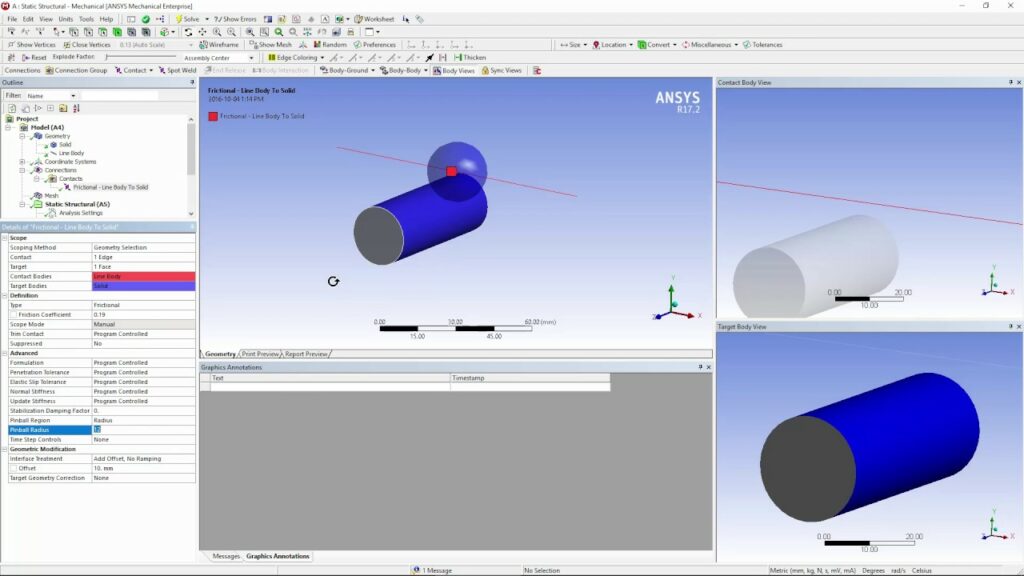
Implementing contact mechanics in ANSYS simulations involves modeling and analyzing the interaction between solid bodies or components that come into contact during mechanical operations. Contact mechanics simulations are essential for understanding frictional forces, stresses at contact interfaces, wear patterns, and overall structural behavior under realistic loading conditions. ANSYS provides sophisticated tools and capabilities to accurately simulate and analyze contact interactions, ensuring robust design and engineering of components across various industries. This comprehensive guide will cover the theory, setup procedures, contact types, modeling techniques, analysis methods, interpretation of results, advanced considerations, and applications of contact mechanics in ANSYS simulations.
Table of Contents
- Introduction to Contact Mechanics in ANSYS Simulations
- Fundamentals of Contact Mechanics
- Setting Up for Contact Mechanics Simulations
- Types of Contact in ANSYS
- Contact Modeling Techniques
- Performing Contact Mechanics Analysis in ANSYS
- Interpreting Contact Mechanics Results
- Advanced Considerations in Contact Mechanics
- Best Practices for Contact Mechanics Simulations
- Applications of Contact Mechanics in ANSYS
- Conclusion
1. Introduction to Contact Mechanics in ANSYS Simulations
Contact mechanics in ANSYS simulations involves studying the interaction between two or more bodies subjected to contact forces, frictional effects, and deformation at contact interfaces. This analysis is crucial for predicting structural integrity, wear patterns, fatigue life, and optimizing designs across mechanical, aerospace, automotive, biomedical, and civil engineering applications.
2. Fundamentals of Contact Mechanics
- Contact Interface: Surface interaction between bodies under normal and tangential forces.
- Friction: Resistance to relative motion between contacting surfaces, characterized by friction coefficients.
- Contact Pressure: Distribution of normal pressure and stress at contact points or surfaces.
- Contact Stiffness: Elastic behavior and deformation response during contact interactions.
3. Setting Up for Contact Mechanics Simulations
- Geometry Preparation: Import or create solid models of contacting bodies in ANSYS Workbench or Mechanical.
- Mesh Generation: Generate finite element meshes with appropriate refinement near contact interfaces.
- Material Assignment: Define material properties including elasticity, plasticity, and friction coefficients for each contact body.
4. Types of Contact in ANSYS
- Bonded Contact: Surfaces are permanently attached, assuming no relative motion.
- Frictional Contact: Includes both frictionless and frictional contacts with specified friction coefficients.
- No Separation Contact: Prevents separation between bodies unless a separation condition is reached.
- Rigid Contact: Idealizes one or more bodies as rigid, interacting with deformable bodies.
5. Contact Modeling Techniques
- Surface-to-Surface Contact: Mesh-based contact formulation where surfaces interact directly.
- Node-to-Surface Contact: Node-based contact formulation using discrete contact points.
- Automatic Contact Detection: ANSYS automatically detects and establishes contact pairs based on proximity and overlap criteria.
6. Performing Contact Mechanics Analysis in ANSYS
- Contact Setup: Define contact pairs, contact types, and contact behavior (bonded or frictional).
- Load Application: Apply loads, displacements, or boundary conditions to simulate realistic operating conditions.
- Solver Settings: Configure analysis settings, convergence criteria, and solution controls (e.g., time steps for dynamic analysis).
7. Interpreting Contact Mechanics Results
- Contact Pressure Distribution: Visualize and analyze pressure contours at contact interfaces.
- Frictional Forces: Evaluate frictional forces and moments generated due to relative motion at contact surfaces.
- Contact Area and Gap Analysis: Monitor contact area evolution and gap formation or closure during simulations.
- Wear and Damage Prediction: Predict wear patterns, fatigue damage, or material deformation due to repeated contact.
8. Advanced Considerations in Contact Mechanics
- Nonlinear Contact: Address large deformations, material nonlinearities, and contact stiffness variations.
- Transient Contact: Simulate dynamic or transient contact events such as impacts, collisions, or sliding contacts.
- Surface Treatment Effects: Consider surface roughness, coatings, or lubrication effects on contact behavior and friction.
9. Best Practices for Contact Mechanics Simulations
- Validation: Validate contact models against experimental data or analytical solutions.
- Mesh Sensitivity: Perform mesh convergence studies to ensure accurate stress and displacement predictions at contact interfaces.
- Parameter Sensitivity: Assess sensitivity to material properties, friction coefficients, and contact algorithms.
10. Applications of Contact Mechanics in ANSYS
Contact mechanics simulations in ANSYS find diverse applications:
- Mechanical Engineering: Evaluate bolted joints, gears, bearings, and mechanical assemblies.
- Aerospace Engineering: Analyze landing gear, aircraft structures, and satellite deployments.
- Biomedical Engineering: Study joint mechanics, prosthetics, and orthopedic implants.
- Civil Engineering: Assess soil-structure interactions, bridge bearings, and seismic structures.
11. Conclusion
Contact mechanics simulations in ANSYS are indispensable for predicting and optimizing the behavior of interacting surfaces and components under various loading conditions. By leveraging ANSYS’s advanced simulation capabilities and contact modeling techniques, engineers can enhance product performance, durability, and reliability across diverse engineering disciplines. Mastering contact mechanics enables engineers to mitigate risks of failure, optimize designs, and deliver innovative solutions that meet stringent design requirements and exceed customer expectations. Effective implementation of contact mechanics simulations contributes to advancing technology, improving safety, and achieving engineering excellence in complex mechanical systems and structures.