PowerMill Ultimate: Unleashing the Fifth Dimension – A Comprehensive Guide to 5-Axis Toolpath Creation
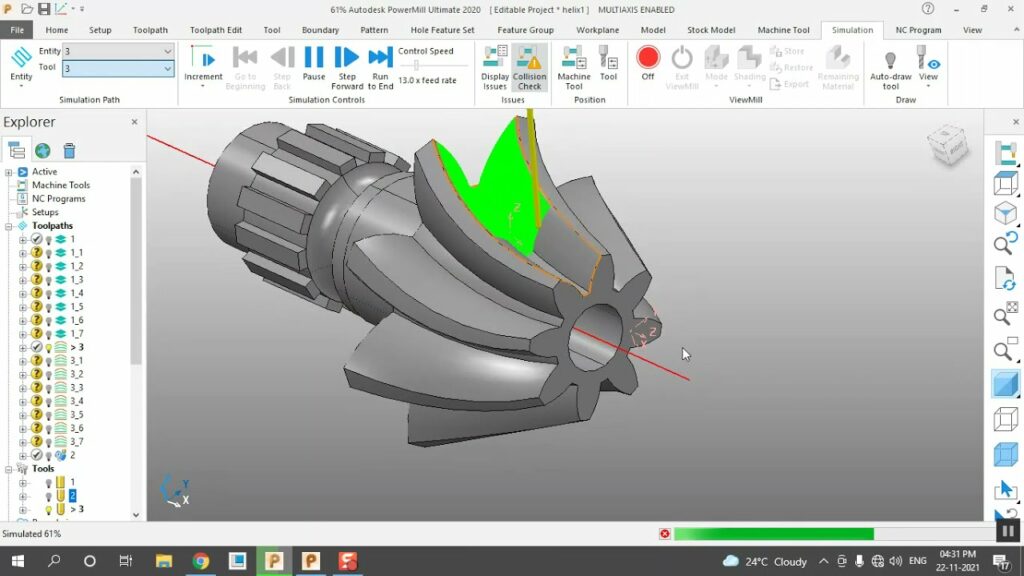
PowerMill Ultimate transcends the limitations of 3-axis machining, empowering you to create sophisticated 5-axis toolpaths. This unlocks a new realm of machining possibilities, enabling you to tackle complex geometries, achieve superior surface finishes, and optimize machining efficiency for a wider range of parts. This comprehensive guide delves into the world of 5-axis toolpath creation in PowerMill Ultimate, equipping you with the knowledge and techniques to navigate the fifth dimension and elevate your machining capabilities.
Understanding the 5-Axis Advantage: Why Embrace More Axes?
Traditional 3-axis machining restricts tool movement along the X, Y, and Z axes. While effective for many applications, it can struggle with complex geometries or features with deep undercuts or internal cavities. 5-axis machining introduces two additional rotary axes (typically A and C) that allow the cutting tool to tilt and rotate around the workpiece, providing significantly greater access and maneuverability. This translates into several key advantages:
Machining Complex Geometries: 5-axis toolpaths can navigate intricate shapes and challenging features that would be impossible or highly inefficient to machine using only 3 axes. This opens doors to machining complex parts like turbine blades, impellers, and molds with intricate details.
Superior Surface Finish: By constantly re-orienting the cutting tool for optimal chip removal, 5-axis machining can achieve smoother surface finishes compared to 3-axis approaches. This is particularly beneficial for parts requiring a high aesthetic quality or those with tight tolerances.
Reduced Setups and Improved Efficiency: 5-axis machining often allows you to machine complex features from a single setup, minimizing the need for multiple setups and repositioning of the workpiece. This translates to faster machining times and reduced overall production costs.
Shorter Toolpaths and Reduced Tool Wear: By optimizing tool engagement and minimizing tool deflection, 5-axis machining can lead to shorter toolpaths and consequently less tool wear. This translates to extended tool life and reduced tooling costs.
By embracing 5-axis toolpath creation in PowerMill Ultimate, you unlock a new level of machining versatility and efficiency, enabling you to tackle even the most challenging parts with confidence.
The Building Blocks of 5-Axis Toolpaths: Essential Concepts
Before delving into specific creation techniques, it’s crucial to understand the core concepts that govern 5-axis toolpath generation:
Machine Kinematics: PowerMill requires an accurate representation of your 5-axis CNC machine’s kinematic configuration (how the axes move and interact with each other). This information ensures the generated toolpaths are physically achievable by your specific machine.
Tool Axis Control: 5-axis machining relies on defining the orientation of the cutting tool throughout the toolpath. PowerMill offers various methods for specifying tool axis control, including:
- Tool Center Point (TCP) Programming: This method directly defines the path of the tool’s center point along the 5 axes.
- Tool Normal and Approach/Retract Strategies: This approach specifies the desired orientation of the cutting tool relative to the machining surface, allowing PowerMill to calculate the corresponding tool center point path.
Collision Avoidance: With more axes in play, collision avoidance becomes even more critical. PowerMill’s collision detection functionalities are crucial for ensuring the toolpath doesn’t interfere with the machine itself, fixtures, or other components.
Crafting Your 5-Axis Arsenal: Toolpath Strategies for Different Applications
PowerMill Ultimate offers a diverse range of toolpath strategies specifically designed for 5-axis machining:
3+2 Machining: A popular approach that utilizes 3 linear axes (X, Y, Z) for primary positioning and 2 rotary axes (A & C) for continuous tool orientation adjustments. This strategy is well-suited for machining contoured surfaces and pockets with varying depths.
Wall Milling: This strategy follows a defined wall or surface along the 5 axes, ideal for machining parts with complex walls, such as turbine blades or mold cavities.
Flowline Milling: A high-efficiency strategy that utilizes a smooth, continuous toolpath around the workpiece, particularly effective for roughing and finishing operations on complex geometries.
Impeller Milling: A specialized strategy designed for machining the blades of impellers and blisks, ensuring smooth transitions and optimal surface finishes.
Multi-Axis Drilling: PowerMill allows for defining drilling operations along 5 axes, enabling precise hole creation on angled surfaces or in hard-to-reach locations.
By understanding these core concepts and the available toolpath strategies, you can select the most appropriate approach for your specific machining needs and desired outcomes.