How to Validate and Verify Simulation Models in ANSYS
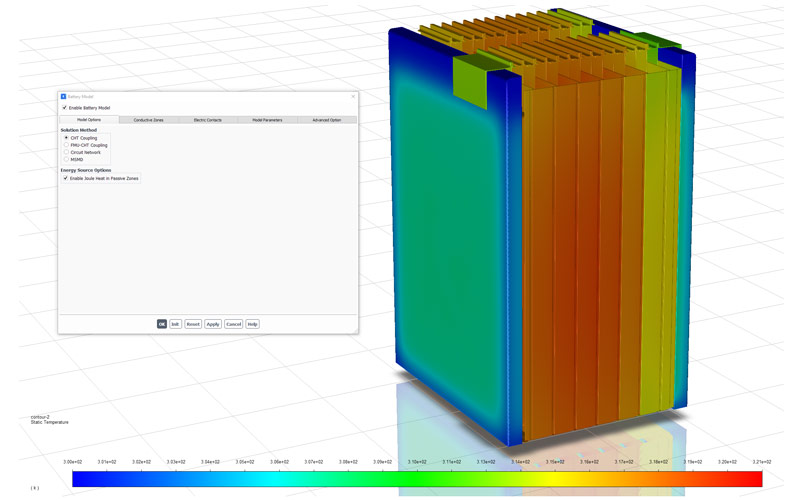
Validating and verifying simulation models in ANSYS is a critical process to ensure accuracy, reliability, and credibility of engineering analyses and predictions. Validation involves comparing simulation results against experimental data or established analytical solutions, while verification ensures that the simulation model accurately represents the intended physical system or phenomenon. This comprehensive guide will cover the principles, methods, procedures, best practices, challenges, and applications of validating and verifying simulation models in ANSYS.
Table of Contents
- Introduction to Validation and Verification of Simulation Models in ANSYS
- Principles of Validation and Verification
- Steps for Validating Simulation Models
- Techniques for Verifying Simulation Models
- Comparison with Experimental Data
- Comparison with Analytical Solutions
- Best Practices for Validation and Verification
- Challenges in Validation and Verification
- Applications of Validation and Verification in ANSYS
- Conclusion
1. Introduction to Validation and Verification of Simulation Models in ANSYS
Validation and verification (V&V) of simulation models in ANSYS are essential processes to establish confidence in computational results. Validation ensures that simulations accurately reflect real-world behavior, while verification confirms the correctness of the simulation model itself. Both processes are crucial for making informed engineering decisions, optimizing designs, and ensuring the reliability of simulation predictions.
2. Principles of Validation and Verification
- Validation: Comparison of simulation results with experimental data or empirical evidence to assess the model’s predictive accuracy.
- Verification: Confirmation that the simulation model is implemented correctly and represents the physical system accurately.
3. Steps for Validating Simulation Models
- Define Validation Objectives: Clearly specify the goals and metrics for validating the simulation model.
- Select Validation Cases: Choose benchmark cases or experiments with well-documented data for comparison.
- Setup Simulation: Configure ANSYS model with appropriate geometry, mesh, material properties, and boundary conditions.
- Run Simulation: Perform simulations under conditions identical to experimental setups or benchmark scenarios.
- Compare Results: Analyze and compare simulation outputs (e.g., stress, displacement, temperature) against experimental measurements.
4. Techniques for Verifying Simulation Models
- Code Verification: Check the correctness of ANSYS software implementation through analytical solutions or method of manufactured solutions (MMS).
- Grid Convergence: Perform mesh refinement studies to ensure simulation results converge to a consistent solution as mesh density increases.
- Parameter Sensitivity: Assess the influence of model parameters (e.g., material properties, boundary conditions) on simulation outcomes.
5. Comparison with Experimental Data
- Data Acquisition: Obtain experimental data using sensors, tests, or measurements under controlled conditions.
- Data Processing: Process experimental data to ensure accuracy and consistency in comparison with simulation outputs.
- Error Analysis: Quantify discrepancies between simulation and experimental results using statistical methods (e.g., error norms, confidence intervals).
6. Comparison with Analytical Solutions
- Analytical Models: Use analytical solutions derived from fundamental principles or simplified assumptions to verify simulation results.
- Benchmark Problems: Solve benchmark problems with known solutions to validate numerical methods and simulation accuracy.
7. Best Practices for Validation and Verification
- Document Methodology: Document simulation setup, assumptions, and validation criteria to ensure transparency and reproducibility.
- Peer Review: Review simulation results and validation methodology with colleagues or subject matter experts for feedback and validation.
- Validation Metrics: Define quantitative metrics (e.g., error tolerance, correlation coefficients) for assessing simulation accuracy.
- Iterative Improvement: Iteratively refine simulation models based on validation results and feedback to enhance accuracy and reliability.
8. Challenges in Validation and Verification
- Experimental Variability: Address variability in experimental data due to measurement errors, environmental conditions, or material properties.
- Model Complexity: Manage complexities in simulation models, including nonlinearities, multiphysics interactions, and transient phenomena.
- Resource Intensiveness: Allocate resources (time, budget, computational power) effectively for comprehensive validation and verification studies.
9. Applications of Validation and Verification in ANSYS
Validation and verification in ANSYS are applied across various industries and engineering disciplines:
- Automotive: Validate crash simulations, durability predictions, and vehicle dynamics.
- Aerospace: Verify structural integrity, thermal analysis, and aerodynamic simulations.
- Biomedical: Validate medical device simulations, biomaterial studies, and tissue mechanics.
- Civil Engineering: Verify seismic analysis, structural stability, and geotechnical simulations.
10. Conclusion
Validation and verification of simulation models in ANSYS are fundamental processes for ensuring the accuracy, reliability, and trustworthiness of computational results. By systematically comparing simulation outputs with experimental data or analytical solutions, engineers can validate the predictive capabilities of ANSYS models and verify the correctness of model implementations. Effective V&V practices enable engineers to make informed decisions, optimize designs, and deliver robust solutions that meet performance requirements and exceed expectations in diverse engineering applications. Continuous improvement in V&V methodologies contributes to advancing simulation technology, enhancing safety, and driving innovation in engineering design and analysis with ANSYS software.